The process of making Powdered Metal Parts
The powdered metal process (metallurgy) allows for creating of these intricately designed metal components by compacting metal powder in a customer designed mold then sintering to create the specified material properties.
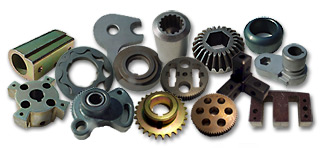
By using different types of metallic powder – including elemental, pre-alloyed, and partially alloyed – manufacturers can achieve a wide range of specific metal compositions. Some common materials used in this process include:
• Copper
• Iron
• Steel
So next time you come across a product made from finely crafted metal, know that it was likely created through powder metallurgy.
Why it needs to be done
Have you ever wondered how various metal parts are formed, such as the gears in a car or the jet engines used in airplanes?
The answer is powder metallurgy. By combining different materials, manufacturers can create strong and durable parts with precisely controlled properties.
Powder metallurgy is a cost-effective and efficient way of producing metal components. It also allows for flexibility in design and the creation of complex shapes that may not be possible through traditional manufacturing methods.
Overall, powder metallurgy is a crucial process for the automotive and aerospace industries. Without it, many everyday objects would not exist.
Benefits of using powdered metal
There are many benefits to using powder metallurgy, including the following:
• Cost savings: Powder metallurgy is a cost-effective manufacturing method.
• Flexibility: This process allows for the creation of complex shapes and designs.
• Precision: Powder metallurgy creates parts with precise compositions and properties.
• Strength: Powder-metal parts are solid and durable.