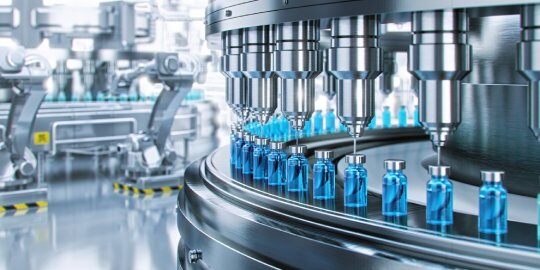
At PSM Industries Inc., our focus on metal injection molding medical technology (MIM) allows us to produce intricate and durable metal parts that meet the demands of the medical sector. This innovative process blends the versatility of plastic injection molding with the strength of metal, enabling the creation of complex components that are essential in modern medical applications.
Understanding Metal Injection Molding in Medical Applications
Metal injection molding medical technology (MIM) is a unique manufacturing technique that involves compounding fine metal powders with a polymer binder to create a moldable feedstock. This feedstock is essential for forming components with exceptional complexity and precision. The MIM powder metallurgy process is particularly advantageous for crafting parts with complex geometries and tight tolerances, which can be challenging to achieve using traditional metalworking methods.
The adaptability of MIM powder metallurgy allows for the use of various metal grades, including a wide variety of stainless steels, which are commonly required in the medical field. These materials not only offer mechanical strength but also ensure biocompatibility and resistance to corrosion, crucial factors for medical devices that come into contact with the human body.
The Metal Injection Molding Process
The metal injection molding medical process at PSM Industries consists of several key steps:
- Feedstock Creation: Fine metal powders, such as high strength alloy and stainless steels, are mixed with a binder to form a malleable feedstock, essential for producing complex medical parts like surgical instruments and medical devices.
- Injection Molding: The feedstock is heated and injected into molds designed to your component design specifications, ensuring intricate designs and tight tolerances.
- Debinding: The solidified part undergoes debinding in a vacuum chamber where the parts are heated in a solvent, where the binder, where the binder is removed, preserving the part’s shape while eliminating excess material.
- Sintering: The debound part is heated to high temperature in a vacuum furnace with a hydrogen backfill atmosphere to the fuse metal particles, enhancing its mechanical properties for reliable performance in medical devices.
- Surface Coating: TFinally, we can apply surface coatings as your requirements require, such as passivation or nickel or chrome plating, to enhance corrosion resistance or improve aesthetics. The choice of coating depends on the intended application and environmental factors, ensuring that the final product meets all necessary performance and regulatory standards.
Advantages of Metal Injection Molding in the Medical Field
Metal injection molding offers several advantages over traditional manufacturing methods. One of the most significant benefits is the ability to produce high-precision parts with minimal material waste. This cost-effectiveness is especially valuable when compared to producing a precision component that requires multiple CNC machining steps.
MIM also provides unmatched design freedom, allowing engineers to create highly complex parts that would be impossible to manufacture using conventional techniques. This flexibility can lead to innovative solutions in medical device design, ultimately improving patient care and outcomes.
The mechanical properties of MIM components are another key advantage. By achieving a uniform microstructure during the sintering process, MIM powder metallurgy parts exhibit higher strength, improved ductility, and excellent surface finishes. These properties are essential in applications where reliability and performance are critical, such as surgical instruments and specialized medical devices.
Why Choose PolyAlloys Industries for Your Medical MIM Needs?
Our technological expertise in metal injection molding powder metallurgy positions us as a leader in providing high-quality metal components for medical applications.
Feel free to contact us and learn more about how our metal injection molding medical services can support your medical device manufacturing needs. Our team is ready to collaborate with you to create custom solutions that ensure quality, precision, and reliability in your products at an economical price.