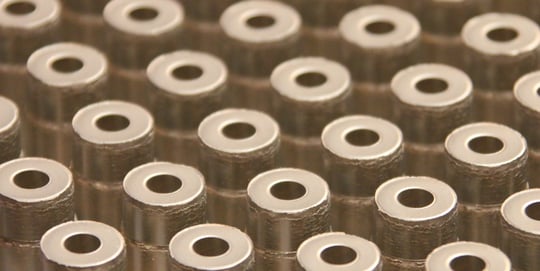
Metal Injection Molding (MIM) is a process that ingeniously combines the versatility of plastic injection molding with the robustness and integrity of metal. By doing so, it offers a groundbreaking approach to part fabrication.
We at PSM Industries harness this innovative process to fabricate intricate and durable metal parts that cater to a variety of applications. We offer a commitment to excellence and technological prowess that sets us apart from our competition. With a focus on quality, precision, and customer satisfaction, we have positioned ourselves as a leader among metal injection molding companies. We consistently work towards delivering solutions that exceed our clients’ expectations across automotive, aerospace, electronics, and telecommunications.
Understanding the Metal Injection Molding Process
The metal injection molding process is a hallmark of PSM Industries' dedication to innovation and precision. At the core of this unique process is the preparation of a unique blend. This is where fine metal powders are combined with a polymer binder to create a moldable ‘feedstock.’ With this feedstock, it’s possible to form components with unparalleled complexity and precision.
The metal injection molding process is similar to plastic injection molding, but the results offer the additional strength and resilience of metal. Thanks to the process and the synergy between the materials, it’s possible to deliver components with intricate designs and high dimensional accuracy. The metal injection molding process offers unmatched versatility, allowing us to work with a variety of metal grades. This includes the robust stainless steel all the way to the conductive copper.
Metal injection molding is particularly advantageous for crafting parts with complex geometries and tight tolerances. These parts would often be a challenge, if even possible, to achieve through traditional metalworking processes.
The beauty of the metal injection molding process lies in its ability to not only replicate intricate details but be able to maintain this consistently across a high-volume production run. Therefore, MIM is the optimum choice for industries that require parts with precision and consistent quality.
The process is adaptable to a wide range of metal alloys. This opens the door to a substantial amount of applications across diverse industry sectors. MIM stands out for its ability to meet these varied and specific requirements, whether it’s durable parts for automotive applications or lightweight components for the aerospace industry.
Advantages of Choosing Metal Injection Molding
Metal injection molding holds several advantages over traditional manufacturing processes. Therefore, it is the preferred choice for a significant number of applications. Let’s break down the key benefits:
Reduced Production Costs
Cost-effectiveness is one of the most important benefits on offer. This is particularly noticeable when producing small and intricate metal parts. MIM tends to minimize material waste and reduce labor costs compared to CNC machining and other traditional methods. It streamlines the manufacturing process and allows for the economical production of high-volume complex parts. Therefore, it's a viable option for businesses wishing to optimize their production budget.
Increased Design Freedom
Metal injection molding provides unparalleled design flexibility. The flexibility allows engineers and designers to create highly intricate metal parts with complex geometries and detailed features. This would otherwise be impossible to achieve through forging, casting, and other conventional methods. The increased design freedom also opens up a world of new possibilities in product development.
Improved Mechanical Properties
Opting for metal injection molding over traditional methods often provides results with superior mechanical properties. By achieving a uniformed microstructure in MIM parts, the results are higher in strength, have better ductility, and an excellent surface finish. The enhanced mechanical properties are desirable in industries where reliability and performance are paramount, like in aerospace, medical, and automotive applications.
Increased Production Efficiency
MIM is renowned for its efficiency, significantly reducing the time from design to production compared to other metalworking methods. This efficiency is particularly evident in mass-producing parts with consistent quality and precision. The MIM process streamlines production, allowing faster turnaround times and enabling companies to meet market demands promptly.
Detailed Walkthrough of the Metal Injection Molding Process
The metal injection molding process is meticulous. It involves an advanced procedure that consists of several key steps. Here’s an insight into what PSM Industries can offer you:
Feedstock Creation
The process begins by expertly mixing finely powdered metal with a specialized binder material. This mixture forms a malleable feedstock, which is the foundation of the MIM process. This feedstock is crucial as it must be precisely formulated to ensure optimal flow and molding characteristics, enabling the creation of complex shapes with fine details.
Injection Molding
The feedstock is then fed into the injection molding machine. This is where it is heated and injected into the mold before cooling and solidifying in the desired shape. This step is important for achieving the intricate geometries and tight tolerances which are associated with metal injection mold parts. The mold design is vitally important as it directly influences the part’s final shape and surface finish.
Debinding
The solidified part is heated in a furnace to remove the binder material. By doing so, the binder material vaporizes, leaving behind a porous metal structure. The debinding stage is delicate. The process must be thorough enough to remove the binder but gentle enough to ensure the part’s shape is not tampered with.
Sintering Process
The metal part of the is then heated to a high-temperature through the sintering process. This enables the metal particles to fuse together to create a solid and long-lasting structure. The sintering process is an important stage to help the part reach its desired mechanical properties like hardness and tensile strength.
Surface Coating
Finally, a surface coat is applied to the sintered part. This can be for aesthetic reasons to improve the appearance of the part or it can be for function reasons, such as enhancing the part’s resistance to corrosion. The choice here will depend on the intended use of the part and the environment it operates in.
Why Choose PSM Industries for Metal Injection Molding?
By opting for PSM Industries for your metal injection molding, you’re choosing a leader in the field to push the limits of your products. We offer an unwavering commitment to quality and innovation, which subsequently places us at the forefront of the industry. With our team of dedicated experts, top-tier customer service, and a broad range of services, we can reach your project’s full potential together.
We will continue to advance MIM technology and provide cutting-edge solutions for various intricate applications. Contact us today to begin a partnership towards the future of metal fabrication and experience firsthand how our expertise can enhance your projects.